質子交換膜(PEM)電解水技術具備電流密度高、運行壓力高且可差壓運行、功率調節范圍寬等顯著優勢,與風電和光伏具有出色的適配性,市場潛力巨大。然而,在當下國內制氫電解槽行業競爭日益激烈的態勢下,堿性電解槽成本已然降至 1000 元/kW 的水平,而 PEM 電解槽卻仍在 3000 - 5000 元/kW 左右居高不下,致使 PEM 電解槽在國內頗有英雄無用武之地之感。在PEM電解槽技術降本的路徑當中,提升電流密度乃是公認的首要方案。那么,提升 PEM 電解槽電流密度應當從哪些角度去考慮和設計呢?
PEM電解槽電流密度可達到的上限
陽極催化劑和膜電極決定了電流密度所能達到的上限,國內科研單位和企業對此研究最為深入,在 2024 年,電解槽普遍能夠達到 2A/cm?以上的應用水平。在催化劑方面,文獻報道其技術水平在 6 - 10A/cm?,然而到了膜電極的匹配性驗證步驟,部分催化劑的性能無法通過考驗。在整個驗證過程中,較為困難的是尺寸的放大,此過程中因尺寸引發了電場、流場等新的變化。由于電極尺寸會致使電場分布不均勻、大電極存在不同的傳質行為,所以小電極上的催化性能難以轉化為大尺寸的高電流密度催化性能。因此,需要更為高效、更節省時間的穩定性和耐久性測試方法,以加快驗證的迭代速度。

(圖:從催化劑到PEM電解槽的電流密度水平)
另一方面,更薄的質子交換膜對于電流密度的提升有著顯著的益處。傳統的 N115 膜是一種較為穩妥的選擇,然而在挑戰高電流密度時,顯然需要將質子交換膜薄到極致,無論是否使用增強層,未來的 PEM 電解水質子交換膜極有可能下探到 50μm 以下的尺度。
影響提升電流密度的設計
首先,在 PTL 的設計方面,要考慮更為嚴苛的氣液傳質情況。高電流密度不僅會帶來劇烈的傳質,還伴隨著散熱的增加。不僅要計算反應耗水,還要解決局部過熱的問題。高電流密度對 PEM 水電解槽的影響在于,由于質子轉移,散熱主要發生在膜上,而后由于界面中的電子轉移,散熱發生在催化層上。必須去除產生的多余熱量,以在約 90°C 的最高閾值溫度下保持常用的 PFSA 基膜的熱穩定性。另外,熱管理對于防止全氟磺酸(PFSA)聚合物膨脹、催化劑降解以及機械應力可能產生的熱梯度至關重要。
其次是體系電阻,在升高電流密度的情況下,體系內的電阻是更為敏感的因素。一般來說,膜的占比最高,膜電阻>界面接觸電阻>電極和金屬板本體電阻,膜電阻常常也等同于體系內部的離子傳輸電阻。PEM 電解槽在這一點上與堿性電解槽有很大的不同,暫時不需要考慮電流密度增加造成的氣泡墻問題。但也需要警惕氣泡過多對水傳輸的影響,有一些具有梯度的 PTL 設計用于解決這一問題。
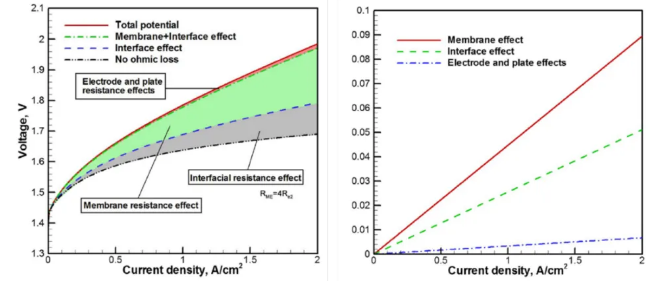
(圖:電解槽影響內阻的主要因素)
提升電流密度后對電解槽的其他影響
除了前面提到的氣液管理,提升電流密度后的滲氫會顯著增加。根據實際經驗,電密由低到高的過程中,氧中氫的含量是逐漸降低的。結合一些文獻的報道,我們發現,這一規律僅在一定范圍內有效。滲氫的通量是隨著電流密度的增加持續增加,由于總反應量的放大,造成一定范圍內氧中氫隨電密增大而減小。然而在更大的電密范圍內,過飽和效應會使得氧中氫濃度也隨著電密增大而增大。
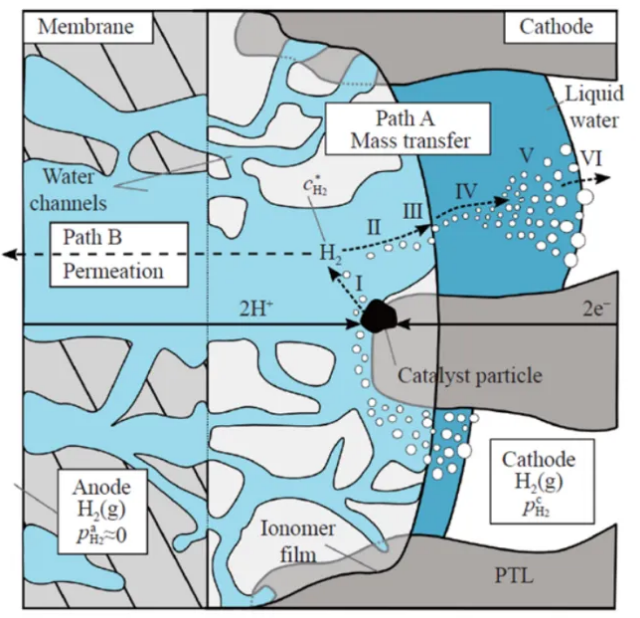
(圖:氫氣的過飽和滲透)
在工程問題方面,提升電流密度還會對鍍層穩定性、PTL 層穩定性等提出更高的要求,這需要引起研發人員的重視,給出令人信服的測試結論。
綜上所述,PEM 電解槽在未來達到 5A/cm?以上的水平已經具備材料基礎。在制氫裝備的產品研發上,需要針對電解槽工程設計和可靠性調試開展更細致的工作。
未來三一氫能將繼續圍繞圓形槽、方形槽、PEM 槽、BOP 的“3+1”技術路線,不斷完善并強化集成設計、材料研發、仿真分析、試驗驗證、電氣控制、制造工藝、氫安全設計七大能力。三一氫能期待與行業客戶、設計院、供應商、科研院所、行業機構等進一步加強合作,達成氫能裝備的高質量發展,為實現“雙碳”目標奉獻三一的力量和三一方案。